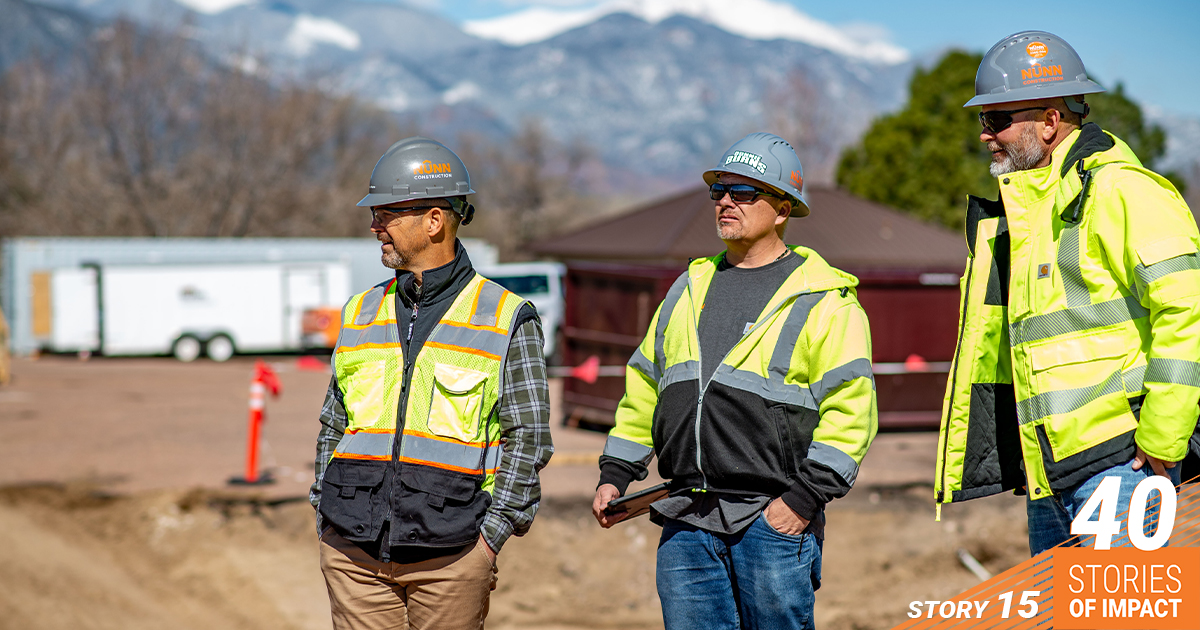
Why is safety important? Put simply, we value people and safety protects people. This value is the foundation that supports all things safety at Nunn and must be strong. Nunn’s safety program is built on this value, acting as the supporting frame for the culture. To create this culture, we rely on our entire team to value safety and utilize the tools we have set in place.
FORECASTING AND REDUCING RISK
While safety has always been a necessity for Nunn, our safety program has truly been streamlined within the last few years. Much of this success can be attributed to leaders who set the framework and the dedication of our full time Safety Manger, Donnie Burns.
Donnie’s journey from Warehouse Manager to Safety Manager was catalyzed by a motocross accident that left him in a wheelchair for 8 weeks. His recovery afforded him time to take safety courses. Years later, Donnie is now a certified OSHA and CPR instructor and has certified 71 people in OSHA 10, 24 in OSHA 30, and 43 in CPR.
“From other job experiences I had, and seeing the hazards that the trades face,” Donnie said, “I wanted to be able to reduce the risk at Nunn.”
Using the safety program established by Nunn leadership, Donnie built upon that foundation by bringing accident prevention to the forefront. By increasing the focus on processes and having a dedicated Safety Manger, Nunn achieved a 2022 EMR rating of .67, the best a company of our size can achieve.
CONSISTENCY IS KEY
A solid safety program is all about consistency in both safety standards and in messaging to employees. At Nunn, that consistency takes the form of a safety program that includes multiple safety committee meetings a month, regular jobsite inspections, and implementation and changes as needed to the current program—amongst many other facets. A recent alteration to our program includes new incentives for employees through quarterly safety awards, certificates of recognition, enhanced gifts, and more.
“Safety is all of our responsibility,” states Tyson Nunn. He asserts that consistency of a safety program comes with the implementation. The worst thing a construction company can do, he says, is have an inconsistent safety program, whether that takes the form of not living the values preached or the uneven execution of the program. Tyson takes his role in championing safety seriously with regular visits to jobsites with Donnie to both “see Donnie in action” as well as to further understand where he can lend his support to the safety program.
But a culture of safety is not just a top-down objective; it must be enveloped and adopted by everyone on the jobsite. Taylor Tafoya, a Carpenter Foreman at Nunn, claims that the culture of safety here is “night and day” compared to other construction companies he has worked for previously. He attributed this difference to the transparency of Nunn’s safety culture and to the commitment of Donnie, VP of Operations Phil LaSarre, and other leadership to the safety program. Other companies that Taylor had previously worked for approached safety with a “brush it under the rug” approach to violations, which directly contrasts with Nunn’s prompt handling of any safety risks.
“Safety is all of our responsibility.”
USING THE RIGHT TOOLS
Constructing an effective safety program is impossible without the proper tools. In Nunn’s toolkit, we utilize external auditors who identify potential blind spots in our safety program. Nunn views our relationship with OSHA as a working partnership for our constant improvement rather than an adversarial authority. We leveraged their wealth of knowledge by receiving a voluntary safety audit in 2022, which was beneficial for enlightening both areas of strength and opportunities for improvement.
Along with OSHA, we utilize the assistance of Mike Rosser with Corporate Safety Services. Mike, having been an immeasurable assistance to us since 1998, performs regular inspections on our jobsites. With his unbiased view of safety best practices, he has been able to assist us to align our safety program with those standards. These audits aid us to form, what Mike calls an “outstanding safety program.”
A culture of safety does not form overnight. It takes the entire team to value it and to see safety as not just a good way to build but the only way to build. Seeking opportunities for continued growth in safety culture is vital. As Tyson says, “You’ll never arrive with safety – you always need to improve.”